The Beneteau Group’s flagship brand Monte Carlo Yachts reveals the innovative way its superyachts are built
Monte Carlo Yachts’ rise from nothing to one of Europe’s leading luxury yacht builders has been as rapid as it has been remarkable. In just over a decade, it has gone from an idea on a blank sheet of paper to building a seven-strong range of semi-custom yachts from 65ft luxury cruisers to 105ft superyachts.
Even experienced industry watchers have looked-on agog as year after year it rolled out ever bigger, ever more complex yachts that would have taken most yards twice as long to develop. MCY’s former boss Carla Demaria would simply nod conspiratorially and say it was all down to the unique secret build process that the team have developed for its facility in Monfalcone, Italy. Only now has MCY agreed to reveal how the magic happens.
The key to MCY’s speed and efficiency is not a single ‘magic bullet’ but a series of innovations that has enabled it to reduce build times and improve quality. It claims that the time and money saved is what allows it to invest so heavily in the finish and customisation for which it is renowned.
The build process is split into three separate elements: the hull, the deck and the interior. Crucially, all three parts are worked on simultaneously so that they are completed at the same time. Only then are the three sections slotted together like pieces of a 3D jigsaw.
What makes this process unique is how far the build goes before the three sections come together. We’re not talking about slotting-in partially completed cabins or lowering a half-finished deck moulding onto a hull; each of the three sections are fully fitted out. All that remains to be done is bonding the sections together and hooking-up the plumbing and electrics. If this sounds too simplistic it’s worth looking in more detail at what’s involved.
The hull
Instead of moulding a hull and then strengthening it with internal grids, bulkheads and stiffeners, Monte Carlo Yachts design the whole thing as a single monocoque structure with built-in rigidity. This is not only quicker and easier to build but it takes up less space than a conventional grid, leaving more internal volume and headroom in the cabins.
Article continues below…
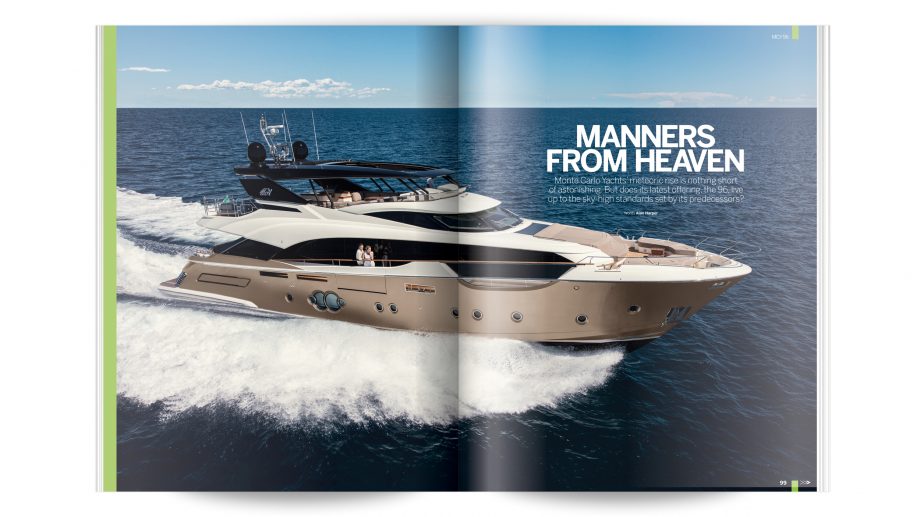
MCY 96 review: Opulent deck spaces cap off this superlative superyacht
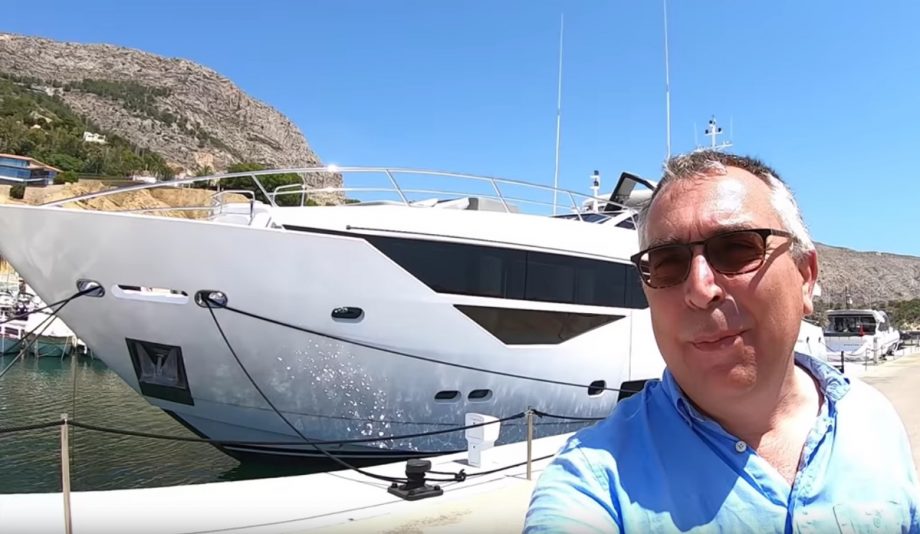
Sunseeker 116 yacht tour: Inside a raised pilothouse superyacht
It creates the necessary strength by using a combination of self-supporting cored GRP mouldings and an aluminium skeleton along with built-in longitudinal stringers and stainless steel engine supports. All the GRP elements are vacuum infused with extensive use of carbon and Kevlar reinforcement.
A substantial crash box in the bow provides additional strength in this high-stress area along with a sacrificial crumple zone should the worst happen. Almost uniquely in the marine industry the entire hull and all the individual mouldings receive a post-curing heat treatment in the purpose-built paint hall, which doubles as a giant oven.
Once the structure is complete, the empty hull is fully fitted out with engines, plumbing, electrics, tanks and the specially insulated engine room bulkheads. The entire forward section, however, is left empty ready for the interior module to be lowered into it.
The interior
Monte Carlo Yachts isn’t the only yard to build its interiors outside the boat (Bavaria also slots partially completed cabins into the hull), but it’s the only one to do so on such a big scale using a single modular structure. The backbone of the system is an aluminium skeleton that looks like a series of interconnected boxes.
Being modular, the size and shape of these boxes can be adapted to take account of different layout options, so long as the main exterior dimensions remain the same. This explains how MCY can offer multiple cabin and layout options at relatively low cost.
With access to every part of the interior, even service areas normally hidden behind bulkheads, it’s far quicker and easier for craftsmen to fit the complex pipework and cabling as well as the normal furniture, fittings and linings. It also enables them to reach the underside of cabins to add insulation and soft mountings to prevent noise and vibrations being passed through the structure and into the accommodation.
Although the process is hi-tech, the materials used and the craftsmanship involved are as traditional as they come, with everything being manufactured in-house using natural stone, solid woods and the best quality leathers.
The deck
The final piece of the jigsaw is the deck, flybridge and superstructure. Again, this is all resin-infused with localised Kevlar reinforcement. The flybridge T-Top itself is pure carbon fibre to minimise weight up top and reduce the boat’s tendency to roll. As with the hull and interior, it is fully fitted out right down to the teak decks, flybridge furniture and electronics for the outside helm station.
Final assembly
The assembly itself is so quick as to be almost anticlimactic. The entire interior is lowered into the hull before being bonded into place. The modular skeleton ensures it fits perfectly with tolerances of no more than a few millimetres. The process is then repeated with the deck.
Plug and play systems mean that all the plumbing and electrics join up so that the whole boat is up and running in a matter of hours. A rigorous system of checks ensures everything is working before the completed boat is wheeled into the paint shop for its final exterior finish. This also explains why customers have a free rein when it comes to hull colours.
Whether this build process results in a better quality boat, a better value boat or simply a more efficient, more profitable yard is hard to quantify.
There’s no doubting that the finished products look and feel as well-built as anyone else’s, albeit not noticeably superior to the construction methods of older, more established yards.
However, in recent years Monte Carlo Yachts has also become increasingly reticent about revealing the prices of its boats to anyone other than seriously interested customers, quoting the need to retain its competitive edge.
Whatever the true value of the advantage, there is no doubt that revealing the secrets of the build process only helps to boost public interest in this growing yard.
First published in the October 2018 edition of Motor Boat & Yachting.